Druckunternehmen stehen oft vor der Frage nach dem ideal geeigneten Verfahren zur Herstellung von Verpackungen und Etiketten. Die Berücksichtigung von Kriterien wie Qualitätsansprüche, Auflagenhöhe, Budget und Terminplanung bietet dabei eine wirksame Unterstützung.
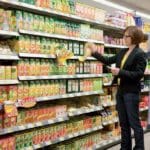
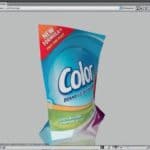
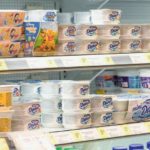
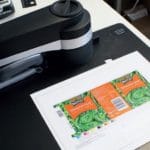

Geschrieben von Geert de Proost
Inhaltsverzeichnis
Die Druckverfahren – Digitaldruck, Flexodruck, Tiefdruck und Offsetdruck
Konventionelle Druckverfahren: Vorteile und Herausforderungen
Drucken im erweiterten Farbraum: Esko Esquinox und der Flexodruck
Unterstützung aller Druckverfahren
Rentabilität: Digitaldruck kontra Flexodruck, Tiefdruck und Offsetdruck
Die Druckverfahren – Digitaldruck, Flexodruck, Tiefdruck und Offsetdruck
Beim Drucken von Etiketten und Verpackungen wird zwischen digitalen und konventionellen Druckverfahren unterschieden: Digital auf Digitaldruckmaschinen und konventionell meistens im Flexo-, Tief- und Offsetdruck. Im Laufe der Jahre haben insbesondere der Digital- und Flexodruck wesentliche Verbesserungen erfahren, wobei jedoch bei beiden Verfahren einige wichtige Für und Wider bestehen bleiben. Bevor Druckdienstleister und Verarbeiter eine Entscheidung treffen, sollten sie diese Vor- und Nachteile der jeweiligen Technologie sorgfältig abwägen, und sich genau überlegen, was sie benötigen oder erwarten, um den Druckauftrag auszuführen.
Kleinauflagen im Verpackungsdruck als Fürsprecher für den Digitaldruck
Druckereien und Verarbeiter müssen sich am Kunden orientieren und dessen spezifische Anforderungen erfüllen. Einer der deutlichsten Trends der vergangenen fünf Jahre ist die schrumpfende Auflagenhöhe. Diese Entwicklung ist auf eine grundlegende Änderung im Kundenverhalten zurückzuführen. Kurz gesagt, der Endnutzer möchte die Wahl haben. Beispielsweise möchte der Verbraucher nicht nur ein einziges Salat-Dressing, sondern gleich mehrere Geschmackssorten davon im Regal vorfinden.
Das bedeutet für den Etiketten- und Verpackungsdruck, dass heute 23 Produktvarianten gedruckt werden müssen, wo früher ein Produkt ausgereicht hatte. Das heißt aber auch, dass die typische Auflagenhöhe durch 23 geteilt werden muss: Statt einer Million Verpackungen bestellt der Druckeinkäufer jetzt für jede der 23 Produktvarianten nur noch 43.000 Verpackungen. Zudem verkürzen spezielle Marketingkampagnen, die um die Aufmerksamkeit des Verbrauchers buhlen, die Lebensdauer eines Etiketts oder einer Verpackung.
Es gibt immer mehr „limitierte Editionen“ bestimmter Produkte oder Verpackungen, die für ein zeitlich begrenztes Angebot stehen. Auch das führt zu kleineren Auflagen und kann sich auch auf die Zeitspanne, in der die Druckerei und der Verarbeiter die Verpackung liefern müssen, auswirken.
Ein weiterer Grund für die steigende Nachfrage nach kleineren Auflagen besteht darin, dass die Markeninhaber und Hersteller auf „Print-on-Demand“ setzen. Niemand möchte mehr große Bestände vorhalten, denn die damit verbundenen Kosten sind einfach zu hoch. Hier sind Just-in-Time- Lieferungen, die gerade ausreichen, den aktuellen Bedarf zu decken, das wirtschaftlichste Konzept.
Zu guter Letzt wollen Markeninhaber bereits in einer frühen Phase des Lebenszyklus ihrer Produkte mit wirklichkeitsnahen Modellen arbeiten. Das bedeutet, dass für Marketingtests und Freigabeprozesse eine sehr geringe Stückzahl produziert werden muss. Erst wenn die Markteinführung des Produkts ansteht, werden größere Mengen bestellt.
Automatisierung beseitigt Engpässe. Nicht nur beim Digitaldruck.
Die genannten Trends werden letztendlich die Investition in eine oder mehrere Digitaldruckmaschinen erforderlich machen, die die in den Drucksälen bereits vorhandenen konventionellen Druckmaschinen ergänzen. Allerdings sollte die Druckerei auch die Auswirkungen des Digitaldrucks auf ihr Geschäft insgesamt überprüfen. Welche neuen Märkte können mit diesen digitalen Kapazitäten erschlossen werden?
Welche neuen Chancen eröffnen sie möglicherweise? Und welchen Einfluss haben diese zahllosen Kleinauflagen auf die Arbeitsabläufe im Unternehmen? Kleinauflagen können ohne eine angemessene Workflow-Automatisierung schnell unrentabel werden. Da verbringt man eine Stunde mit dem Kunden, eine weitere Stunde in der Druckvorstufe und schon ist der Gewinn größtenteils aufgebraucht, noch bevor überhaupt gedruckt wird. Dieser Engpass wird durch die eingeschränkten Kapazitäten in Verwaltung und Druckvorstufe verursacht, die nicht dafür geschaffen wurden, eine wachsende Anzahl von Kleinaufträgen zu bewältigen.
Daher ist die Automatisierung der Verwaltung und der Druckvorstufe der Schlüssel zur Verarbeitung einer viel größeren Anzahl von Aufträgen und eine Notwendigkeit, um die Kapazität insgesamt zu erhöhen und zu optimieren. So bietet die Firma Esko Automatisierungslösungen an, die diese potenziellen Engpässe beseitigen und damit ermöglichen, Kosten einzusparen und die Produktivität zu steigern. Das gilt sowohl für digitale als auch für konventionelle Druckverfahren.
Hier kann ein Management-Informationssystem (MIS) Wunder wirken und diese administrativen Engpässe vermeiden. Die Automatisierung der Druckvorstufe verringert die Fehlerwahrscheinlichkeit und erhöht die Produktivität, da manuelle und sich wiederholende Aufgaben vermieden werden. Die Automatisierung der Druckvorstufe und der Verwaltung ist die Voraussetzung, um die Anlagen maximal auszunutzen.
Konventionelle Druckverfahren: Vorteile und Herausforderungen
Konventionelle Druckverfahren wie Offset- und Flexodruck werden vor allem wegen der Kosten- und Produktivitätsvorteile sowie zuweilen auch wegen der besseren Qualität insbesondere für hohe Auflagen eingesetzt. Bei der Nachbestellung bereits gedruckter Aufträge wird man in nahezu allen Fällen das ursprünglich verwendete Druckverfahren weiter nutzen, damit diese Nachdrucke stets die gleiche Qualität aufweisen.
Jedoch erfordern konventionelle Druckverfahren, unabhängig ob im Flachdruck oder Hochdruck, einen höheren Rüstaufwand, da die Farbe erst während der Einrichtung abgestimmt und die Anlage auf das optimale Druckergebnis und Druckbild kalibriert wird. Daher gehört die Umrüstzeit zu den wichtigsten Kriterien, wenn es darum geht, konventionelle und digitale Druckverfahren miteinander zu vergleichen, denn schließlich geht diese beim Auftragswechsel im Digitaldruck praktisch gegen null.
Deshalb sollten die Druckereien auch die Gesamtbetriebskosten berücksichtigen. Dazu gehört ein unzulässig hoher Makulaturanfall von teuren Medien als Nebenprodukt langwieriger Maschinen-Rüstzeiten.
Drucken im erweiterten Farbraum: Esko Esquinox und der Flexodruck
Eine Möglichkeit, diese Herausforderung teilweise zu bewältigen, besteht darin, einen unveränderlichen Farbensatz mit einer festen Farbpalette zu verwenden. Das kann dazu beitragen, die Umrüstzeit zu verkürzen, die Produktionsprozesse zu rationalisieren und die Kosten für das Farblager zu senken. Esko Equinox bietet sich an, um im erweiterten Farbraum zu drucken und die Qualität und Effizienz des konventionellen Flexodrucks zu erhöhen.
Drucken im erweiterten Farbraum bedeutet, dass die Verpackung nicht in CMYK-Farben und mit den jeweils zusätzlich benötigten Schmuckfarben produziert wird, sondern dass die Druckmaschine von vornherein auf einen Satz aus fünf, sechs oder sieben Farben eingerichtet wird. Üblicherweise kommen CMYK plus zwei oder drei weitere Farben, wie Orange, Grün oder Blau, zum Einsatz.
Mit dieser Erweiterung des traditionellen CMYK-Farbraums können die Druckereien mit weniger Farben, weniger Druckplatten, kürzeren Rüstzeiten und einer höheren Produktivität bessere Farben erzielen. Gleichzeitig werden die Qualität und Konsistenz verbessert. Damit kann die Druckerei exakt auf den Bedarf der Markeninhaber reagieren, die die Kosten senken wollen, ohne Kompromisse bei der Farbtreue eingehen zu müssen. In vielen Fällen gewährleistet dieses Verfahren sogar eine bessere Druckqualität und ein besseres Farb-Druckbild.
Was die Druckform betrifft, versetzt – neben Equinox – Full HD Flexo von Esko die Druckereien und Verarbeiter in die Lage, den konventionellen Flexodruck für Etiketten und Verpackungen auf das Qualitätsniveau von Offset und Tiefdruck anzuheben – ein Heiliger Gral für den Flexodruck.
Esko Full HD Flexo ist ein Herstellungsverfahren für digitale Flexodruckplatten. Die optimierten Platten gewährleisten auch auf preiswerteren Substraten eine höhere Qualität mit brillanten Farben sowie eine konsistentere Druckqualität als digitale Flexo-Standardplatten.
Unterstützung aller Druckverfahren
Letzten Endes geht es bei der Entscheidung zwischen konventionellen und digitalen Druckverfahren darum, ob die betreffende Technologie die Anforderungen der Kunden erfüllen kann. Zu diesem Zweck müssen effiziente und durchgehende Workflows in Verwaltung und Produktion eingerichtet sein, die unabhängig vom verwendeten Druckverfahren reibungslose, effiziente und rentable Arbeitsabläufe sicherstellen.
In diesem Artikel wurden bereits einige Lösungsansätze vorgestellt. Es gibt jedoch noch weitaus mehr Strategien, die geeignet sind, ein Druck- oder Verarbeitungsunternehmen zu optimieren, damit es die Anforderungen des heutigen dynamischen Marktes erfüllen kann.
So ermöglichen Softwarelösungen zum Erfassen von Managementdaten den Maschinen, die Geschäfts- und Produktionsprozesse zu rationalisieren. In diesem Zusammenhang sind digitale Technologien, wie CTP, Digitaldruckmaschinen, Prüfsysteme, Farbsysteme und digitale Verarbeitungsgeräte eine Voraussetzung, um dieses Ziel zu erreichen. Eine weitere Möglichkeit, den Kosten- und Zeitaufwand unabhängig vom Druckverfahren zu verringern, besteht darin, virtuelle 3D-Visualisierungen zu nutzen. Sie erlauben, das Produktdesign mit verschiedenen Veredelungstechniken unter einer Vielzahl von Lichtbedingungen dreidimensional darzustellen.
Diese Lösungen können sogar zeigen, wie das Produkt im Verkaufsregal im Vergleich zu den Waren der Mitbewerber aussieht. Es ist auch wichtig zu berücksichtigen, dass die moderne Produktion für gewöhnlich mit Anlagen und Software arbeitet, die von zahlreichen unterschiedlichen Anbietern stammen. Auf dem sich rasant ändernden Druckmarkt mit seinen Kleinauflagen ist es unverzichtbar, dass alle diese Systeme nahtlos und reibungslos zusammenarbeiten.
Heute sind die Unternehmen auf eine beispiellose Workflow- Automatisierung mit einer robusten Qualitätskontrolle angewiesen. Dieser Herausforderung müssen sich die Druckereien und Verarbeiter stellen.
Rentabilität: Digitaldruck kontra Flexodruck, Tiefdruck und Offsetdruck
Bei bloßer Betrachtung der Stückkosten ist der Digitaldruck immer noch erheblich teurer als konventionelle Druckverfahren. Das gilt insbesondere für die verwendeten Farben. Die Farbkosten sind ein wichtiges Kriterium, das bei einem Vergleich der Rentabilität von digitalen und konventionellen Druckverfahren zu berücksichtigen ist.
Die Kosten pro Druckexemplar liegen im Digitaldruck weitaus höher, dafür sind aber die Rüstkosten viel niedriger. Und genau am Schnittpunkt dieser beiden wichtigen Gesamtstückkosten-Linien werden konventionelle Druckverfahren wirtschaftlicher. Allerdings dürfen der Abfall, der durch einen veralteten Lagerbestand bedingt ist, sowie die Vorteile des Digitaldrucks beim Print-on-Demand ebenfalls nicht vergessen werden.
Mit anderen Worten: Bei der Entscheidung für oder gegen digitale und konventionelle Druckverfahren müssen die Gesamtkosten des Lebenszyklus und nicht nur die hinter der Druckmaschine anfallenden Stückkosten beachtet werden. Heute liegt der mittlere Schnittpunkt im Bereich von 1500 bis 2500 Laufmetern. Natürlich kann sich dieser Wert in Abhängigkeit von bestimmten Variablen, wie der Bahnbreite, den Farben, der Druckgeschwindigkeit und den Qualitätsanforderungen, die in diesem Artikel angesprochen wurden, ändern.
Ein Trend, der bisher noch nicht genannt wurde, betrifft die wachsende Nachfrage nach variablen Daten auf Etiketten und Verpackungen. Diese werden für gewöhnlich in Form von Barcodes oder Zahlen aufgebracht. Für diese Projekte ist der Digitaldruck häufig die bessere Wahl, da er die variablen Daten in einem Durchgang drucken kann. Die Etiketten müssen also nicht in einem separaten und fehleranfälligen sowie zeitraubenden Prozess auf die Verpackung aufgebracht
Aufgrund der Vorteile, wie kleinere Auflagen, weniger Abfall durch veraltete Lagerbestände, verbesserte Zykluszeiten, das Inline-Drucken variabler Daten und minimale Umrüstzeiten, die der Digitaldruck bietet, können digital produzierte Aufträge häufig zu einem Premiumpreis verkauft werden. Viele Druckereien sehen in der Digitaldruckmaschine jedoch nur eine weitere Anlage und bedenken nicht, dass sich ihr Verkaufskonzept oder Preismodell ebenfalls ändern muss. Wie in diesem Beitrag bereits erwähnt, bieten digital gedruckte Materialien einen eindeutigen Mehrwert.
Wenn der Verkaufsprozess und das Preismodell entsprechend angepasst werden und digital gedruckte Materialien nicht mehr ausschließlich nach dem Preis beurteilt werden, wie es bei konventionellen Druckverfahren häufig der Fall ist, wird sich die Rentabilität des Digitaldrucks mit Sicherheit weiter erhöhen.
Zusammenhänge erkennen
Viele Zulieferer unternehmen große Anstrengungen, um Lösungen auf den Markt zu bringen, die sowohl digitale als auch konventionelle Druckverfahren für Etiketten und Verpackungen unterstützen.
So informiert beispielsweise Esko Druckereien, Verarbeiter und Markeninhaber umfassend über neue und verbesserte Technologien und Lösungen, die die gesamte Lieferkette von Etiketten und Verpackungen rationalisieren können und allen Beteiligten Zeit-, Kosten- und Qualitätsvorteile bieten.
Heute und in Zukunft sind Automatisierung, Zusammenarbeit, Visualisierung und kundenspezifische Anpassung Schlüsselwörter, die für alle Drucktechnologien gelten.
Anmerkung der Redaktion: Verfahren wie Siebdruck oder Buchdruck spielen beim Verpackungsdruck eine eher untergeordnete Rolle.